EOTPR 4000 Electro Optical Terahertz Pulse Reflectometry
Electro Optical Terahertz Pulse Reflectometry(EOTPR): The world’s fastest and most accurate fault isolation system.
The EOTPR 4000 system is configured with an automated probe station which is capable of placing the probe tip to +/- 5 μm precision, while maintaining the EOTPR’s world leading sub-5 μm fault isolation accuracy.
This combination allows users to directly probe TSV tips and copper pillars.
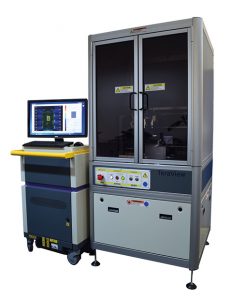
Key Features
• Pre-scan station to map contact location and height.
• Data acquisition time of less than 5 seconds per pin.
• Software that will drive the automated probe station and pre-scan station.
• Availability of both manual mode and automated mode for probing.
• User interface software to manage data display and recipe creation.
• Probe tip placement.
Key Components
• 5 μm accuracy auto-prober.
• Pre-scan station for contact point mapping.
• Automated probe station that can also be operated in manual mode.
• EOTPR probe head.
Core Unit
• THZ source: Laser gated photo-conductive semiconductor emitter
• THz detector: Laser-gated photo-conductive semiconductor detector
• Laser: Ultra short pulsed laser
• A/D converter: 16 bit
• TDR pulse rise time: 6 ps (based on processed data) Defined as the time for the reflected impulse from the end of the high frequency probe to rise from 10 % to 90 % of its maximum value
• Accuracy: Able to locate a feature on 50 Ω coplanar waveguide positioned close to the high frequency probe with precision of ± 5 µm
• Range: Up to 270 mm from contact with probe on a 50 Ω strip line
• Input impedance: 50 Ω nominal
• Channel input connector: 1 mm
• Probe configuration: In addition to fitting within the TeraView supplied station, the probe is suitable for mounting on the Alessi REL-4800 parametric probe station made by Cascade Microtech (not supplied)
• Dimensions (ex. probe station): 600 mm (w) x 1320 mm (h) x 1000 (d) mm
• Weight (ex. probe station): 220 kg (480 lbs)
• Electrical power requirements (ex. probe station): 90 VAC to 250 VAC, 47 to 63 Hz single phase
• Operating temperature: 18 °C (64 °F) to 30 °C (86 °F)
• Operating humidity: Up to 80 % (non-condensing)
Automated Probe Station
• Probe station modes of operation: Auto BGA probing (for BGA > 200 μm), semi-auto probing mode (see specifications below) or manual probing mode
• Probe tip pitch: 30 μm to 1.2 mm with compatible GGB and Cascade probes
• Probe tip calibration: Quick probe calibration to determine:
• Position of the signal and ground tips
• Probe tip pitch
• Device under test size: 5 mm x 5 mm to 70 mm x 70 mm
• Device mounting: Devices under test are mounted to the probe station with reusable Gel-Pack mounts
• Device under test contact type: Compatible with BGA, LGA and microbumps
• Minimum solder ball diameter: 30 μm (semi-auto mode)
• Minimum LGA pad size: 30 μm x 30 μm (semi-auto mode)
• Device under test pre-scan time: Less than 60 seconds (single 16 mm stripe)
• Measurement time per pin: Less than 5 seconds (no co-averaging)
• Software: A full software suite to enable data collection and analysis with the automated probe station
• Data file format Data files will contain the
• following information:
• Device name/type (user specified).
• Pin locations measured.
• Measured date.
• Task information/comments (user specified).
• Microscope: Microscope supplied with CCD camera
• Dimensions (estimated): 1000 mm (w) x 1900 mm (h) x 900 (d) mm
• Weight (estimated): 250 Kg
• Environment: As per the core unit
This combination allows users to directly probe TSV tips and copper pillars.
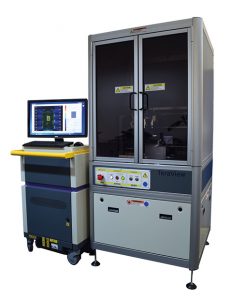